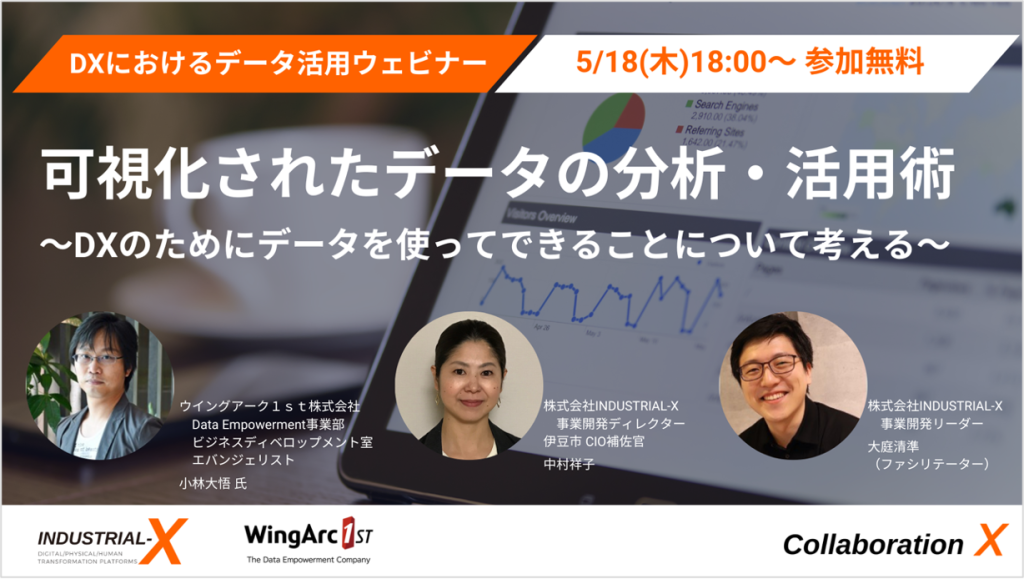
【イベントレポート】Collaboration X vol.2 可視化されたデータの分析・活用術
〜DXのためにデータを使ってできることについて考える〜
オンライン・INDUSTRIAL-Xオフィス
DXにおけるデータ活用の重要性(INDUSTRIAL-X 中村)
改めまして、INDUSTRIAL-X事業開発ディレクターをしております中村祥子と申します。
本日は、DXにおけるデータ活用の重要性をお話いたします。
簡単に私の自己紹介をさせていただきます。
2000年4月に日立ソフトウェアエンジニアリングというSIerの会社に入りまして、19年ほどシステムエンジニアをしてました。
その後、グローバルで働きたいと思い立ち日本マイクロソフトの方に転職し、シニアコンサルタントカスタマーサクセスマネージャーを務めました。
多角的な提案ができる仕事をしたく、INDUSTRIAL-Xに、昨年の11月から参画しました。
「未来に向けた産業構造改革変革をともに」をビジョンにしている、INDUSTRIAL-Xは、2019年4月に設立され、代表を八子が務めており、DX、IoTなど様々な分野で活躍しています。
(INDUSTRIAL-X:https://industrial-x.jp/)
皆さんが散々聞いてるDX(デジタルトランスフォーメーション)とは何か改めて振り返ります。
DXとは、情報システムを刷新する話ではなく、いかにデジタル技術を活用して業務やビジネスモデルを変革し、変革して市場の供給に応えていくこと。
デジタルトランスフォーメーションですが、トランスフォーメーションが主であって、やはりデジタルは、活用するものです。
今の時代、何もしないでいると、周りが動いているので、どんどん自分が下がっていくのが現状です。
現状維持は、下りのエスカレーターに乗ってるようなものです。
労働人口が減少する日本において、絶対にやっていかないといけないことは生産性向上です。
投下労働量を下げるか、総売り上げを上げるか、もしくは両方一度にやれば生産性は上がります。
両方一度にやると、価値あることを早くいかに売上を上げながら労働力を減らしていくか、早く決めて早くやるスパイラルを早く回すやり方があります。
早く決めるためには、可視化・洞察・検証を早く回す必要があり、いつでもどこでも誰とでも繋がるような仕掛けが必要です。
絶対に分からないといけないものは、データで現在地を知ることです。
そもそも、今どの状況にいるのか?目指す場所までの距離は、遠いのか近いのか。
例えば、交通機関であれば、遠くまで行くとき、新幹線や飛行機を選ぶし、近ければ徒歩で行くように、距離により、手段は変わります。
【事例1】A市でのシステム導入判断
担当者の近隣の中堅都市で市民向けシステムの導入が行われ、「A市でも補助金が出るので、導入してはどうか?」という提案が議員からありました。
初期費用、ランニングコスト、人が張り付く時間を含め、今後長期的に見たとき一番効果が高いものはなにか、それを全て試算して、結局は導入しないことに決めました。
【事例2】家具製造企業の判断
データを活用して、自社の生産データとケアデータを組み合わせて、経営データを組み合わせてBIツールで見える化を行いました。
結果、売上が大きい取引先の現状の取引先価格では採算が合ってないことが判明し、取引を継続しない判断をしました。
データが取れるとデジタルシミュレーションができ、製造工程であれば、製造のラインをもう一つ試すことができます。
データがわかれば、バーチャルの空間でシミュレーションして、その内容を現場に戻すことができます。
デジタルを活用し、新しい売上を生み出すことができる可能性があります。
ビジネスモデルを変革していくために、デジタル技術を活用し、現状を認識し、次にどう生かしていくのか。
この判断のために、いかにデータが取れてるかが必要です。これからビジネスで勝つ上では、データ活用に意思を持つことが、必ず必要になっていきます。
データを共通言語に経営と現場をつなぐ(ウイングアーク1st 小林氏)
ウイングアーク1st(以下、ウイングアーク)の小林と申します。
僕の実体験も含めながら、データは、点在するという意味がなく、繋げないといけないということをテーマにお話します。
以前は、アメリカや、ドイツの製造業の企業で働いていました。
現在は、ウイングアークというデータ活用の会社にいます。
ウイングアークは、ソフトウェアの会社です。大きく分けて二つあり、1個は、帳票見積もりですとか請求書をデザインして出すようなツールと、電帳報対応するような文書管理サービスをやってます。
もう1個が本日の中心になるこちらのデータエンパワーメント事業です。データを溜める・可視化・分析します。
こういう製品を提供しているんですが、本日は製品説明ではなくて、データの話をします。
20年程前に、私が新卒で入った会社で、開発部門にいた時の事例です。
総資産の効率をどれだけ上げられるか、これをどんどん分解していきます。
実は事業本部長が言った「在庫回転率を上げる」のは、実はそのうちの1個になっていて、この左下の方です。
ROA(総資産利益率)目標7%だとしても、ROAに関わる部署は、ほぼ全部です。
営業が売り上げを上げる、工場が設備の効率を上げる、在庫の回転率を上げるのも一つです。
逆もしかりです。不良率20%低減した現場でも、それ低減すると、どれだけコスト削減に繋がるか、わからないですよね。データで繋がってるけれど、指標がバラバラです。
現場力がある日本は、現場にいっぱいデータが埋まっているけれど、あまり経営に使われてないし繋がっていません。
【事例】ヤンマー建機さん(以下、敬称略)
経営者と現場と、DX推進者の3人が、ヤンマー建機がやったことは、データを繋げたことです。
最初にやったこと、これはみんなが個人持ちになってるデータを集めて繋げ、現場の生産性向上を図ることでした。
データをどんどん現場に出させて、弊社のデータベースの「Dr.Sum」(ドクターサム/ウイングアーク社のデータ分析基盤製品)に集めました。
データを繋げるだけ繋げるのは、コストがかかりますが、経営者をうまく巻き込みました。
可視化部分で言うと、BI(ビジネス・インテリジェンス)ツールをやってます。
BIツールは、売上や利益がが落ち込んだ際に、商品別に分解でき、デジタルツインで工場をイメージしてリアルタイムで生産性を可視化することができます。
また、データを入力も可能なため、ドライバーに配送割り当てみたいなアプリも、同じツールで作れます。
先程、品質保証のお話でお金換算したらと話しましたが、これをもっと広範囲でやってます。
部品、品質検査もですが出荷後、お客様に対してサポートをする人件費を含めて、トータルで不良を起こしたら、いくらかかるのかを見ることができます。
集計スピードがすごく早くて、10億件でも1秒で集計可能です。
DX推進は、ツールだけでは足りなくて、ノウハウも必要です。
eラーニングをはじめ、一緒にデータ活用を伴走するようなカスタマーサクセスみたいなサービスも提供しています。
お陰様で、顧客満足度調査で、第1位をいただきました。
いかに現場のデータを集めてきて、それを経営に繋げて、うまくいってるのかをヤンマー建機の事例をもとに説明しました。
クロストーク:お客様事例に学ぶDX時代のデータ収集と具体的活用方法
(ディスカッション・小林氏、中村、INDUSTRIAL-X 大庭*ファシリテーター)
大庭:質問がきています。
データの利活用にあたって、取り組みによる失敗事例や、よくある落とし穴はありますか?
大庭:まずは、私から手元のよくあるミスを共有します。
よくある例ですが、第2次世界大戦の爆撃機の損傷箇所をプロットをイメージした写真です。
これを見たときに、皆さんならどこを修理したいと思いますか?
これは、数字になってないですけど、この赤い点が損傷箇所として、データとして集まっています。
2パターンありますが、
選択肢1:ここの点が集まってる箇所を重点的に直す。
選択肢2:もしくは、それ以外。
(会場参加者に挙手を求め)半々ぐらいですね。
あくまで一例ですが、当時の統計学者の方は赤い点がない、白い方を直しましょうと言いました。
なぜなら、これは帰ってきた爆撃機だからです。
帰ってきているということは、この赤い点のところを打たれても帰ってこれた。
逆にこの頭のプロペラのところや、頭のドアのところとかは、打たれると帰って来れないと、捉え直して、強化するべきはこの当たってない部分だと考えました。
実際に現場で、BIツールを使ったデータの誤解の一例です。
昔のデータで、年収が米国人の年収はこれぐらい上がってることを、ぐっと引き延ばしてすごく急カーブを描いて上がっているように見せる手法があります。
実際小林さんとか、こういう事例とかってあったりしましたか?
小林:確かに社内を説得しようとした時、場合によってはそういった見せ方も有効になりますね(笑)
データの見せ方で結構意図的になっちゃいます。
データの取得と活用フェーズでの落とし穴の事例ですと、まずツールも必要です。
でも、人も、予算もノウハウも必要です。
データ活用は、結構必要になるものがいっぱいあり、この何かが欠けると、大体うまくいかないケースが多いです。
データ活用の推進をされている企業を見ると、そこには中心になる推進者って呼ばれる方がヤンマー建機のように、3名の場合もあります。
この推進者は、色んなものを求められる。
ヤンマー建機であれば、現場に強い方や、経営者も巻き込んで、DXを推進しました。
予算が下りなかったり、現場の反対にあったり、組織横断でやらなきゃいけない。
DX時代のデータ活用だと、うまく周りを巻き込んで必要なノウハウや予算を集めるところが、汎用的な答えとしては、落とし穴になりやすい。
これが抜けてないか、チェックしていただくのがいいです。
大庭:いわゆるデータリテラシーの言葉でよく表現されますが、お客様に提案したり、リテラシー教育に携わることはありますか?
小林:私の場合は製造業のお客様で、いわゆるビジネス成果に相当するところで携わります。
お客様は、データを使って改善することは、やったことがないので、この点をご支援することが多いです。
質問ある方いますか?
質問:実際、データを収集できる環境を作り、分析し、現場に落とし込んでいきます。
この中で、私が一番難しいと感じるのは、データの収集も、実際現場の人からしたら、デイリーオペレーションにプラスなんですね。
例えば、文書をOCRに読み込ませる、このひと手間がすごい現場の負担になる。
推進者からすると、本来やってほしいレベルですが大きな経営のKGIがある中で、目標達成のためにやってくださいと話しても、絶対やってくれない。
そういう反発者っていうのは、どんな組織でも絶対ずっといるし、アナログな業務ができることで自分の存在価値を高めたい人も当然います。
先程、推進者の力量とおっしゃってましたが、推進者次第で、プロジェクトの成否が変わってくることは分かりました。
他に、DX推進に協力してほしいときに、現場の巻き込み方の事例があれば教えてください。
小林:データ活用をしたいと思うとデータを取りたくなります。でも、製造業の現場においては、物の形が変わらないことは全てロスなんですよね。
極端にいうと、一歩歩くのもロスなんですよ。
現場にデータを書かせるのもロスなんで極力なくしてIoTを使いましょう。
他にも、いくつか工夫ができます。現場では指示書を見ながら物を作るので、指示書を電子化するとデータが取れます。
1ページ、2ページとページをめくって次の作業をします。
つまり、今何ページにいるかという、進捗が分かります。ページをめくったら、そのページの作業が終わったことなので、作業時間が分かります。
この作業にかかった時間はデータ入力しなくても、自動的に取れます。
こういう工夫を現場でやり尽くす必要はあります。とは言え、「デジタルなんて」って人はいるんです。
経営者は、課題を見つけて潰すこともありがちで、経営者がこれをやるともう絶対にデータを出してくれなくなる。
僕でも出したくない。
とある経営者が言ってましたが、めちゃくちゃ稼働率上がってるけど、何したのってリアルタイムで聞くとめちゃくちゃモチベーションが上がって、データを上げてくれるようになる。
もう一つの、これは強権的な方法なんですが、アプローチはガバナンスを効かせる。
ちなみにウイングアークはですね、SFA(Salesforce)を導入したとき、当時皆んなExcel管理で、このSFA導入に結構大変だったそうなんです。
SFAに入ってないデータは、会社は案件として認めません。
このように、ガバナンスをかけました。これは結構強力で、そうすると営業の売上数字は、そこに入ってないものは認められません。
でも、逆に営業の業務効率化を少し後押しして、そこに活動履歴を入力したら、週報はSFAから取って自動で出すから、週報書かなくていいです。飴と鞭みたいな話ですが、工夫のしがいがあるところかなと思いました。
大庭:次の質問に移ります。データドリブンを実現するために、経営層や現場を巻き込む事例や方法などありますでしょうか。
中村:現場にデータがあると言われてるけれど、やはり現場には、まだまだデジタル化に慣れていない人はいます。
チェンジマネジメントをやってたりします。
そのときに必要なものは、推進者と同時に、スポンサー。アメリカのデータで、同僚に聞くと聞きやすいということで、「アンバサダー」という仕掛けを作りました。
前職のときに、コロナ禍でMicrosoft「Teams」を展開していくとき、「Teams使ってくださいね」って言っても、慣れない人だと使わない。
若手はSNSとかに慣れてるので、割と使ってくれるけれど、年齢が上がると、そこに対して抵抗感があったりします。
機能も、使い勝手もよくわからない。
気づくとバージョンも上がってる。
そういうときにすぐ聞ける人っていうのを作っておく必要があります。
役員会議とかで、まず上の人に使ってもらうのが重要なので、役員の方に使っていただく。
上の方が使ってれば下は使わざるを得ないっていう状況になるんで上の人に使ってもらう。
役員の人がわからないとき、ちょっとしたことは、隣の役員には聞きに行かず、大体、秘書に聞くんです。
なので、まず一番最初に秘書の方向け勉強会を開催し、ツールの使い方勉強会を役員会議でそのツールが使える状況にしました。
役員も使ってるから現場も使えるでしょうという形にしました。
結果的に会社全体で使うのが当たり前になったのも、うまくいった事例としてあります。
大庭:ありがとうございます。
ちなみに、小林さんは、経営層を巻き込むために踏ん張ったこととか、説得した経験とかあったりしますか。
小林:私は商品企画をやってるんで、商品企画を続けていると、いろいろなツッコミが来るんですよね。
そのときにやっぱりデータの話をしといてなんですが、推進者の人で1個重要なキーワードがあるのは、熱意だと思うんですよね。
データ活用をして、成果が上がって会社が変わるって、DXをやる前から、確実にデータで示せる人っていないと思うんです。
意外とアナログな話ですが、今まで喋ってないところの観点でいうと、熱意があるかな。
大庭:ありがとうございます。私も前職は、社会人の皆さんに、AIや、データサイエンスを教える立場だったんです。
やっぱり最後は、気合いというのは、皆さんお話されてました。
例えば官公庁では、大量にデータがあっても活用できていない状況だったので、皆さんが持ってる気持ちを引き出して、このデータ使えますよと、後から道具を提案するようなやり方はよくやってました。
大庭:最後に1問だけ。
工場内のデータを収集して、行き着く先のイメージを明確にしたいとき、ウイングアーク様で一番進んでる事例を出せるのであれば、お願いします。
こちらは可能でしょうか?
小林:ご紹介するのはヤマハさん(以下、敬称略)の事例です。楽器を作ってるヤマハです。
ヤマハの事例は、ウイングアークの中で10年前と現在と、2回紹介しています。
10年前の取り組み、DXは当然なかったですけど、データ活用の部分が中心かなと思います。
楽器なので、手で組み立てる工程が多いんです。
紙に書いてたやつをExcelに頑張って転記して、何個作りました、不良品が出ました。
紙からExcelに転記するとすごく工数がかかるので、それをレポートにまとめて月次で報告していました。
2つ問題点があって、1つ目は紙からの転記に工数がかかること。
2つ目は月次報告であることから、問題発生から報告までの時差が発生することです。
10年前に取り組んだのは、デジタル化しましょうということで、紙に書いてたやつをタブレット入力に変えて、リアルタイムで集計できるようになりました。
これで入力の手間と、集計レポートを作る手間がなくなりました。
それにより、リアルタイムで問題点に気づけたんでロスが削減できました。
10年前ですが、DXの入口に近いデータのお話です。
ヤマハの場合、特に物量も多く、人の作業も多いので、効果が大きいです。
そこから、10年経って、タブレットに入力します。
今、サックスや、ギターにも、そこにビーコンのデータがついています。
これ作ってくださいねという指示書が、回ってるんですけど、そこに見本のデータがあって作業者もビーコンを持ってます。
それが同じここにいるということは、その時間、その人はそれを作ってたってことがわかるんですね。
これにより、1個作るのに何秒かかったかっていうのを自動収集できるようになりました。
その結果、分析するために、そのビーコンで時刻はわかってるので、遅くなったとか早くなった時刻の映像を、ドラレコみたいに確認することできます。
そこからさらに進んで、デジタルツイン。
現実の工場のデータを収集し、それを仮想工場ってこれがデジタルツイン。
リアルな工場と同じようなものをツール「Motion Board」(モーションボード/ウイングアーク社のBIダッシュボード製品)上で持ってます。
これを出すために、やったことは製造業の方だとわかるんですけどBOM(部品表)やPOP(生産時点情報管理)と呼ばれるマスターの整備です。
工場が違って、データを取る場所とか、この指標を取ろうっていうのを標準化して決めてるので、どの工場であっても同じ生産性の指標が見えてモデル化する、データのモデリングを一生懸命やってやってます。
その結果、まさにシミュレーションを回してこの順番で物を作ったらというのを、シミュレーションを出してその結果実際に工場で走らせて、実際に測っていき、それをぐるぐる回してます。ってこういう部分はする。
工場DXでの究極系だと思います。
特に手組みが多いようなヤマハでできるっていうのは、ここまでできてる会社さんってのはなかなかいないので、僕はすごいなって思ってます。
多分製造業の企業全体っていう意味で見るともうちょっと大きいかなと思うんで、先程DXの定義の中でX(トランスフォーメーション)のところって製造業の生産現場の改善だけじゃないと思うんですよね。
それによってデータ活用で社会を変革したり、顧客に付加価値を提供したり、他社と差別化したり。
そこは業種によらない話なので工場の中でいうと、僕の中での結構ゴールに近い理想形で、10年かけて集大成までいったっていう感じです。
大庭:あそこまでいけるとまさにDXっていう感じがしましたね。
では、もうお時間も参りましたのでこれで最後の質問として終わりにします。
皆さん、改めてご参加ありがとうございました。